Apr 20, 2023 | Blog
Ultraviolet (UV) curing systems have become indispensable in industries like printing, coating, and adhesive applications, primarily due to their ability to rapidly cure materials. These systems harness ultraviolet light, an electromagnetic radiation type characterized by wavelengths shorter than visible light but longer than X-rays. The UV spectrum is generally categorized into UVA, UVB, and UVC, while visible light constitutes a separate category. We’ll explore the distinctions between UVA, UVB, UVC, and visible light in UV curing systems, along with their respective applications and advantages.
The Role of UVA in UV Curing Systems
UVA (320-400 nm) exhibits the longest wavelength range in the UV spectrum and the lowest energy levels among the three UV categories. Owing to its superior penetration depth and reduced potential for substrate damage, UVA is the most widely utilized type of UV light in curing systems. Some of the key benefits of UVA curing systems include:
- Rapid curing times that enhance production efficiency
- Improved adhesion between substrates and coatings or adhesives
- Lower environmental impact due to reduced volatile organic compound (VOC) emissions compared to traditional drying methods
- Enhanced durability and scratch resistance of cured products
The Application of UVB in UV Curing Systems
UVB (280-320 nm) possesses shorter wavelengths and higher energy levels than UVA. While the increased energy makes UVB more efficient at initiating polymerization reactions, it also raises the potential for substrate damage. Consequently, UVB curing systems are not as prevalent as their UVA counterparts. However, they can be beneficial in specific applications where faster curing and higher surface hardness are required, such as:
- Optical fiber coatings that demand increased hardness and durability
- Automotive refinish coatings that need rapid curing times
- Certain industrial coating applications requiring high crosslink densities for improved chemical resistance
UVC’s Limited Use in UV Curing Systems
UVC (200-280 nm) has the shortest wavelengths and highest energy levels within the UV spectrum, rendering it highly effective at breaking molecular bonds and eliminating microorganisms. However, its high energy levels also pose a significant hazard to both materials and human health. As a result, UVC is seldom used in UV curing systems for industrial applications. Instead, UVC is mainly employed in germicidal applications, such as:
- Air purification systems for residential and commercial buildings
- Water disinfection processes in water treatment facilities
- Surface sterilization in healthcare settings and laboratories
Despite limitations in industrial applications, UVC bandwidth can be employed to help overcome oxygen inhibition, producing hard surfaces and high gloss finishes. Oxygen inhibition is a phenomenon that occurs during the UV curing process when oxygen interacts with the free radicals generated by the photoinitiator, inhibiting the polymerization reaction and creating a tacky, uncured surface layer. By utilizing the high-energy UVC wavelengths, it is possible to achieve faster and deeper penetration into the coating or ink, which allows for a more efficient curing process and reduces the occurrence of oxygen inhibition.
The application of UVC in these instances can result in an improved surface cure, characterized by hard, durable surfaces and high gloss finishes. This is particularly beneficial for industries that require high-quality finishes, such as automotive, electronics, and packaging. However, it is essential to carefully manage the potential hazards associated with UVC exposure to ensure the safety of both the materials being cured and the operators working with the UV curing systems.
Visible Light Curing Systems
Visible light (400-700 nm) is a separate category within the electromagnetic spectrum, encompassing wavelengths detectable by the human eye. Although not part of the UV spectrum, visible light can be harnessed for curing purposes in some systems, known as visible light curing systems. These systems typically use photoinitiators that absorb light within the visible spectrum to trigger polymerization reactions. Visible light curing systems are less common than UV curing systems but offer advantages in specific applications, such as:
- Curing UV-sensitive materials that would be adversely affected by UV light exposure
- Achieving greater depth of cure, which is beneficial for thick or highly pigmented coatings
- Reducing the risk of material yellowing, which can occur with some UV-cured systems
Recognizing the differences between UVA, UVB, UVC, and visible light in UV curing systems is crucial for selecting the appropriate technology for particular applications. UVA curing systems dominate the market, offering an ideal balance between penetration depth and substrate safety. UVB and visible light curing systems cater to niche requirements, whereas UVC is primarily reserved for germicidal applications. By understanding the unique properties and applications of each type of light, manufacturers and industry professionals can optimize their curing processes, ultimately improving product performance and operational efficiency.
Apr 13, 2023 | Blog
In the modern, fast-paced business landscape, it has become increasingly important for companies to find ways to optimize efficiency and productivity in order to maintain a competitive edge. With advancements in technology playing a critical role in driving innovation across numerous industries, one such breakthrough that has made a significant impact is the Ultraviolet (UV) curing system. This cutting-edge technology has proven to be a game-changer, particularly in fields such as printing, electronics, and coatings, offering a new level of speed and effectiveness that surpasses conventional methods.
What is UV Curing?
UV curing is a sophisticated process that employs ultraviolet light to rapidly cure or solidify materials such as inks, coatings, and adhesives. As opposed to traditional drying methods, this technique has gained popularity due to its ability to provide a quicker, more efficient, and eco-friendly alternative. By harnessing the power of UV light, businesses can save time, energy, and reduce their environmental impact, making UV curing a preferred choice in a variety of industries.
How Do UV Curing Systems Work?
A UV curing system operates by utilizing three key components: a UV light source, the material to be cured (such as inks, coatings, or adhesives), and a photoinitiator that is incorporated into the material. During the curing process, the UV light source emits ultraviolet radiation, which is absorbed by the photoinitiator present in the material. This absorption of energy triggers the production of free radicals, which in turn initiate a chain reaction known as polymerization. As a result of this rapid reaction, the material transforms from a liquid or semi-solid state into a solid, fully cured form in a matter of seconds or minutes.
The Benefits of UV Curing Systems
Faster Curing Times: One of the most notable advantages of UV curing systems is their ability to cure materials at an incredibly rapid pace. Unlike traditional methods, which may require hours or even days to fully cure materials, UV curing systems can complete the process in a matter of seconds or minutes. This remarkable increase in curing speed leads to significant improvements in production efficiency, allowing businesses to meet tight deadlines and satisfy customer demands more effectively.
Energy Savings: UV curing systems are known for their energy-efficient nature. Since the curing process occurs almost instantaneously, these systems consume considerably less energy than conventional drying methods, which require prolonged heating or air circulation. This reduction in energy consumption not only leads to cost savings but also contributes to a company’s sustainability goals.
Superior Quality: Materials cured with UV technology often exhibit superior physical properties compared to those processed using traditional techniques. These enhancements include greater scratch resistance, increased chemical resistance, and more vibrant coloration. As a result, businesses can achieve a higher quality finished product that meets or exceeds customer expectations.
Environmentally Friendly: Another significant benefit of UV curing systems is their minimal environmental impact. Unlike conventional methods that can produce harmful emissions or volatile organic compounds (VOCs) during the drying process, UV curing systems operate without generating these harmful by-products. This makes UV curing a more environmentally friendly option, aligning with the growing trend towards greener business practices and helping companies reduce their carbon footprint.
Uvitron International
Uvitron International is a leading manufacturer of high-quality UV curing systems, catering to the diverse needs of various industries. Here’s why Uvitron International should be your go-to choice for UV curing solutions:
Cutting-Edge Technology: Uvitron International’s UV curing systems are designed using state-of-the-art components and the latest advancements in technology. This ensures exceptional performance, reliability, and longevity for our systems, providing a solution you can trust.
Customized Solutions: We recognize that each business has its own unique requirements and challenges. That’s why our team of skilled experts works closely with clients to develop tailored UV curing solutions that align with their specific needs and objectives, resulting in optimal outcomes.
Exceptional Customer Support: At Uvitron International, our commitment to customer satisfaction is unwavering. We take pride in offering outstanding customer service, with a dedicated support team that is always available to address any questions, concerns, or technical issues that may arise.
Competitive Pricing: We firmly believe that top-quality UV curing systems should be accessible without breaking the bank. Our dedication to providing exceptional value for our customers means that we strive to offer competitively priced solutions that don’t compromise on quality, making our UV curing systems a wise investment for businesses looking to enhance their productivity and efficiency.
Apr 11, 2023 | Blog
Additive manufacturing, also commonly known as 3D printing, has revolutionized the way industries design, prototype, and produce parts and products. The development of novel materials and techniques has only broadened the potential applications of 3D printing, and one such advancement is the use of ultraviolet (UV) curing.
UV curing refers to the process of using ultraviolet light to harden or cure a liquid or semi-solid material, like a photopolymer resin. When exposed to UV light, the resin’s molecules undergo a chemical reaction, transforming the liquid into a solid plastic or elastomer. This curing process offers advantages like rapid curing times, increased durability, and reduced environmental impact compared to traditional methods.
Enhanced Material Properties
UV curing in additive manufacturing enables the use of advanced photopolymer resins, leading to enhanced material properties. State-of-the-art UV light curing systems, developed by innovative companies in the field, offer customizable solutions that cater to various requirements, from adjustable intensity and wavelength control to precision in exposure time. These advanced systems play a crucial role in optimizing the UV curing process, which in turn increases the mechanical strength, durability, and chemical resistance of printed parts.
By harnessing the power of cutting-edge UV curing technology, additive manufacturing can produce functional prototypes and end-use parts with improved performance and longevity compared to those made from traditional materials. This results in a broader range of applications across industries, including aerospace, automotive, medical, and electronics. The commitment to continuous research and development by industry leaders ensures that the impact of UV curing technology on additive manufacturing will keep evolving and pushing the boundaries of what is possible.
Accelerated Production Times with Uvitron International’s UV Curing Systems
One of the most significant benefits of UV curing in additive manufacturing, facilitated by companies like Uvitron International, is the reduction in production times. Uvitron’s high-performance UV curing systems optimize the curing process, allowing it to be completed in seconds or minutes, depending on the material and part size. This stands in stark contrast to the hours or even days required for traditional curing methods.
The accelerated curing made possible by Uvitron International’s technology enables faster prototyping, which in turn reduces the time-to-market for new products and allows manufacturers to respond more swiftly to changing customer demands. By offering a range of UV curing systems designed to cater to diverse needs and applications, Uvitron International has played a pivotal role in streamlining the additive manufacturing process and driving increased efficiency across various industries.
In the darkest hour of the global pandemic, a new light of hope emerged as innovative solutions were sought to combat the unprecedented challenge of COVID-19. One such extraordinary story is that of Production 3D, a manufacturer of 3D printed products that stepped up to the plate when the world needed them the most. With a heroic mission to create nasal swabs for COVID testing, Production 3D was determined to ensure patient comfort, speedy print times, effective sterilization, and rapid delivery. Discover the incredible story of how Production 3D joined forces with Uvitron and, through their state-of-the-art curing solutions, managed to skyrocket the output of Nasopharyngeal NP Swabs by a staggering 36x, playing a crucial role in the battle against the global pandemic. You can read the case study here: https://www.uvitron.com/blog/a-cure-for-medical-supply-manufacturing-production-3d-case-study/
Enhanced Accuracy and Resolution through Advanced UV Curing Systems
Incorporating UV curing in additive manufacturing allows for high-resolution printing, as the UV light can be focused precisely to cure the material in a highly controlled manner. Advanced UV curing systems, developed by industry leaders like Uvitron International, contribute to this capability by offering precise light control and exposure settings. This results in parts with fine features, sharp edges, and smooth surfaces, making it ideal for intricate and detailed designs.
The increased level of precision brought about by these state-of-the-art UV curing systems has expanded the capabilities of additive manufacturing. This has enabled its use in industries with stringent requirements, such as aerospace, medical, and electronics. The continuous advancements in UV curing technology, driven by companies dedicated to research and development, promise to further refine additive manufacturing processes and unlock new potential applications across various sectors.
Reduced Environmental Impact through Modern UV Curing Systems
The UV curing process in additive manufacturing is generally more environmentally friendly than traditional curing methods, thanks in part to advancements in technology provided by industry leaders. Since the process requires less energy and generates fewer by-products, it leads to a reduced environmental footprint. Advanced UV curing systems have been designed to further optimize energy consumption and minimize waste, contributing to a more sustainable manufacturing process.
Additionally, UV-curable materials often have lower volatile organic compound (VOC) emissions, further reducing the overall environmental impact of the manufacturing process. As the technology continues to evolve, it is anticipated that companies focused on developing and refining UV curing systems will remain committed to enhancing the sustainability and eco-friendliness of additive manufacturing processes.
Emerging Applications and Industries through UV Curing in Additive Manufacturing
The use of UV curing in additive manufacturing has paved the way for new applications and industries, thanks to the ongoing advancements in technology. The combination of high resolution, enhanced material properties, and rapid production times has enabled the creation of complex parts for industries such as dental, jewelry, and automotive. This expansion into diverse sectors showcases the versatility and potential of UV curing in additive manufacturing.
Furthermore, UV curing, such as the solutions provided by Uvitron International, has allowed additive manufacturing to enter the realm of electronics, enabling the production of miniaturized components and printed circuit boards. As UV curing technology continues to evolve, it is expected that additive manufacturing will uncover even more applications and industries, further demonstrating the transformative impact of UV curing on the manufacturing landscape.
In the Whip Mix Case Study, we present a prime example of how Uvitron International’s UV curing systems have been tailored to meet specific client needs. Whip Mix required large UV curing chambers to accommodate customer demand and production needs, while ensuring biocompatibility, shorter curing times, and increased capacity per curing cycle. Dive into this intriguing case study to learn more about Uvitron’s commitment to addressing unique client requirements and delivering exceptional results: https://www.uvitron.com/blog/the-cure-for-dental-difficulties-whip-mix-case-study/
The integration of UV curing in additive manufacturing, made possible by the pioneering efforts of companies like Uvitron International, has had a transformative effect on the industry. Uvitron’s cutting-edge technology has enabled the production of parts with enhanced material properties, accelerated production times, and improved accuracy. Furthermore, Uvitron International’s commitment to developing environmentally-friendly solutions has contributed to the reduced environmental impact of the additive manufacturing process. The newfound applications across various industries, such as aerospace, automotive, medical, and electronics, have expanded the reach and potential of additive manufacturing. As the technology continues to evolve, Uvitron International’s dedication to innovation and growth will ensure that UV curing remains a vital component in the ongoing advancement of the additive manufacturing industry, leading to even more breakthroughs and possibilities.
Apr 3, 2023 | Blog
In recent years, the market for UV light curing systems has experienced unparalleled growth, reshaping the landscape of numerous industries. This cutting-edge technology leverages ultraviolet light to initiate and expedite the curing process of a wide range of materials, including adhesives, coatings, and inks. As a result, UV light curing systems have quickly become an indispensable tool in an array of sectors, such as manufacturing, medical, automotive, electronics, and even the printing industry. The accelerated adoption of UV light curing systems can be attributed in part to the technological advancements from within the industry.
Improved Raw Materials
The development of better and more cost-effective raw materials has played a crucial role in enhancing the efficiency and performance of UV light curing systems. These improvements have not only led to superior results but have also contributed to reduced production costs, making the systems more accessible and affordable for businesses across various industries. Key developments in raw materials include:
Advanced Photoinitiators: Photoinitiators are essential components in UV-curable formulations, as they absorb UV light and generate reactive species that initiate the curing process. Innovations in photoinitiator technology have led to the creation of more efficient, faster-reacting, and less-toxic compounds. These advancements enable better control over the curing process and improved performance in a broader range of applications.
High-Performance Resins: The evolution of resin technology has resulted in the development of high-performance materials with enhanced properties, such as increased adhesion, durability, and chemical resistance. These improvements enable UV light curing systems to cater to a wider array of applications and industries, expanding their overall market potential.
Environmentally Friendly Materials: As environmental awareness grows, the demand for eco-friendly materials has risen. Researchers and manufacturers have responded by developing raw materials that minimize environmental impact without compromising performance. This includes the creation of low-VOC (Volatile Organic Compounds) formulations and bio-based resins that contribute to a more sustainable curing process.
Customizable Formulations: The ongoing development of raw materials has also led to the availability of customizable formulations, allowing businesses to tailor the properties of their UV-curable products to better suit specific applications. This flexibility enables companies to address unique requirements and challenges, further expanding the potential uses of UV light curing systems.
Advanced System Designs
Innovations in system design have significantly contributed to the evolution of UV light curing systems, resulting in more compact, user-friendly, and customizable solutions. These design improvements have made it easier for businesses to adopt and integrate UV light curing technology into their existing workflows, ultimately leading to improved quality and consistency. Key advancements in system design include:
Compact Form Factor: Modern UV light curing systems are designed to be more compact, allowing for easier integration into production lines with limited space. This streamlined form factor enables businesses to implement the technology in a wider range of settings, expanding the potential applications for UV light curing systems.
User-Friendly Interfaces: The introduction of intuitive user interfaces and touchscreen controls has made it easier for operators to interact with and manage UV light curing systems. These user-friendly interfaces simplify the process of adjusting settings, monitoring system performance, and troubleshooting, reducing the learning curve for new users and increasing overall efficiency.
Smart Controls: Modern UV light curing systems often feature intelligent controls that enable better monitoring and regulation of the curing process. These smart controls can automatically adjust light intensity, exposure time, and other parameters to optimize the curing process for specific materials and applications. This level of automation results in improved quality, consistency, and reduced waste.
Customizability: Advanced system designs have also led to more customizable UV light curing systems, allowing businesses to tailor the equipment to their specific needs. This can include features such as adjustable wavelengths, modular components, and the ability to integrate with other production equipment, providing companies with greater flexibility and control over their curing processes.
Enhanced Cooling Systems: As UV LED technology generates heat during operation, the incorporation of advanced cooling systems in modern UV light curing equipment has become essential. These improved cooling systems ensure optimal performance, prolong the lifespan of the LEDs, and prevent potential damage to sensitive materials. Efficient cooling systems also contribute to energy savings and reduced maintenance costs.
IoT Integration and Remote Monitoring: With the growing adoption of the Internet of Things (IoT) in various industries, UV light curing systems have also embraced this trend. Modern systems can be connected to networks, allowing for real-time data collection, remote monitoring, and predictive maintenance. This connectivity enables businesses to proactively address potential issues, minimize downtime, and optimize overall production efficiency.
Safety Features: Advanced system designs have also incorporated enhanced safety features to protect both operators and equipment. These features may include built-in safety interlocks, UV shielding, and automatic shut-off mechanisms that help prevent accidents and unintended exposure to UV light.
Expanded Integration with Automation
As industries continue to adopt automated processes to enhance efficiency and productivity, UV light curing systems have evolved to seamlessly integrate with these advanced workflows. This integration has been crucial in enabling businesses to further optimize their production lines, increase throughput, and reduce downtime. Key aspects of this integration include:
Robotic Integration: UV light curing systems can now be easily integrated with robotic arms and other automated equipment, allowing for precise positioning and movement during the curing process. This level of precision ensures consistent results and enables the curing system to adapt to complex geometries or hard-to-reach areas in the production process.
Automated Material Handling: The incorporation of automated material handling systems, such as conveyors and pick-and-place machines, allows for a streamlined workflow between different stages of the production process, including UV curing. This integration results in a more efficient production line and reduces the potential for human error.
Programmable Logic Controllers (PLCs): Modern UV light curing systems can be integrated with Programmable Logic Controllers (PLCs) and other industrial control systems, enabling businesses to automate and synchronize the curing process with other production stages. This synchronization ensures that the entire production line operates harmoniously and efficiently.
Machine Vision Systems: Integration with machine vision systems allows UV light curing systems to inspect and verify the quality of the curing process in real-time. By detecting defects or inconsistencies early, businesses can make immediate adjustments, minimizing waste and improving overall product quality.
Data Collection and Analysis: As UV light curing systems are integrated with automated processes, they can collect valuable data on production efficiency, curing parameters, and system performance. This data can be analyzed to identify areas for improvement, optimize curing parameters, and support predictive maintenance efforts. By leveraging this data, businesses can make more informed decisions and enhance their overall production efficiency.
Scalability: The seamless integration of UV light curing systems with automated processes also allows for easier scalability. As production demands increase, businesses can effortlessly expand their UV curing capacity by adding additional systems or modules to their existing automated production lines.
Industry 4.0 and Smart Manufacturing: The integration of UV light curing systems with automated processes is in line with the growing trend towards Industry 4.0 and smart manufacturing. By incorporating these systems into connected, data-driven production environments, businesses can benefit from real-time monitoring, adaptive production processes, and increased overall efficiency.
Reduced Labor Costs: Automating the UV curing process eliminates the need for manual intervention, reducing labor costs and the potential for human error. This cost-saving benefit is particularly advantageous for businesses operating in high-volume production environments or those facing labor shortages.
Uvitron: Growing with the Industry
Uvitron, a leading manufacturer of UV light curing systems, has experienced remarkable growth as the industry has expanded. By staying at the forefront of innovation and responding to emerging trends and demands, Uvitron has managed to establish itself as a key player in the market. The company’s success can be attributed to several factors, including its commitment to technological advancement, product diversification, and customer-focused approach.
Commitment to Technological Advancement: Uvitron has consistently invested in research and development, enabling the company to develop cutting-edge UV light curing systems that incorporate the latest technologies. By staying ahead of the curve in terms of technological advancements, Uvitron has been able to provide solutions that meet the evolving needs of industries adopting UV curing processes.
Product Diversification: Recognizing the versatility of UV light curing systems across various industries, Uvitron has expanded its product portfolio to cater to a wide range of applications. This diversification includes systems designed for specific industries. By offering tailored solutions, Uvitron has been able to address the unique requirements of different sectors, further solidifying its position in the market.
Customer-Focused Approach: Uvitron’s commitment to providing exceptional customer support has played a significant role in its growth. The company’s approach to customer service includes offering expert advice, customization options, and after-sales support to ensure customer satisfaction. This dedication to meeting customer needs has helped Uvitron build lasting relationships with clients and foster a positive reputation in the industry.
Adaptability and Agility: As the UV light curing industry has evolved, Uvitron has demonstrated an ability to adapt and respond to changing market dynamics. The company’s agility in recognizing and addressing new trends, such as the growing demand for environmentally friendly and energy-efficient solutions, has been crucial to its success. By being proactive in meeting the needs of the industry, Uvitron has managed to stay relevant and maintain its position as a leading provider of UV light curing systems.
Focus on Quality and Performance: Uvitron’s commitment to delivering high-quality products that provide reliable performance has been a cornerstone of its success. By prioritizing quality and investing in rigorous testing procedures, the company has built a reputation for excellence that resonates with customers across various industries.
Mar 28, 2023 | Blog
The printed electronics industry has seen significant growth over the past decade, with advancements in materials, manufacturing techniques, and novel applications. One technology that has been instrumental in pushing the boundaries of printed electronics is ultraviolet (UV) curing systems. These systems use UV light to initiate a rapid, controlled polymerization process that solidifies inks and coatings on various substrates.
UV curing systems typically consist of three key components: a UV light source, a photosensitive material (such as ink or coating), and a substrate on which the material is applied. The UV light initiates a photopolymerization process that quickly transforms the liquid photosensitive material into a solid, stable form. This curing process provides several advantages over conventional drying methods, such as faster curing times, reduced energy consumption, and increased durability of the printed material.
Benefits of UV Curing Systems for Printed Electronics
Faster production speeds: The rapid curing time of UV-cured materials allows for high-speed printing processes, significantly reducing the time required for each production cycle. This translates to reduced downtime, higher output, and increased capacity to meet growing demand for printed electronics.
Enhanced durability: The UV curing process results in a strong bond between the photosensitive material and the substrate, leading to improved mechanical and chemical resistance. This ensures that printed electronic components can withstand harsh environments, such as extreme temperatures, humidity, and exposure to chemicals, making them suitable for a variety of applications.
Environmentally friendly: UV curing systems consume less energy compared to traditional thermal curing methods, reducing the overall carbon footprint of the manufacturing process. Additionally, since UV-cured materials generate fewer volatile organic compounds (VOCs) during the curing process, there is a significant reduction in air pollution and waste disposal concerns.
Increased design flexibility: UV curing systems enable the printing of intricate patterns and structures on various substrates, allowing for greater design freedom. This facilitates the development of innovative printed electronics solutions, such as conformable sensors, flexible displays, and miniaturized components for various applications.
Applications of UV Curing Systems in Printed Electronics
Printed circuit boards (PCBs): The use of UV curing systems in the PCB manufacturing process has led to significant improvements in resolution and layer alignment. This enables the production of high-density, multi-layer PCBs with smaller feature sizes, which are essential for compact electronic devices.
Flexible electronics: The rapid curing process makes it possible to print electronic components on flexible substrates, such as polyimide films or textile materials. This has opened up new possibilities for wearable devices, medical sensors, and other applications where flexibility and conformability are required.
OLED displays: UV-cured materials can be used to create stable and efficient organic layers for OLED displays, resulting in higher brightness, longer lifetimes, and improved power efficiency. This technology is increasingly being adopted in smartphones, televisions, and other consumer electronics products.
Printed sensors: UV curing systems have facilitated the production of robust, high-performance printed sensors for various applications. Examples include pressure sensors for automotive safety systems, gas sensors for environmental monitoring, and biosensors for medical diagnostics. The versatility of UV-cured materials allows for the development of innovative sensor designs with improved sensitivity and durability.
UV curing systems have already made a significant impact on the printed electronics industry, and their influence will only grow as the technology continues to evolve. The ongoing development and adoption of UV curing systems will facilitate the creation of more efficient, sustainable, and versatile electronic devices and applications, ultimately shaping the future of printed electronics and driving innovation across various industries.
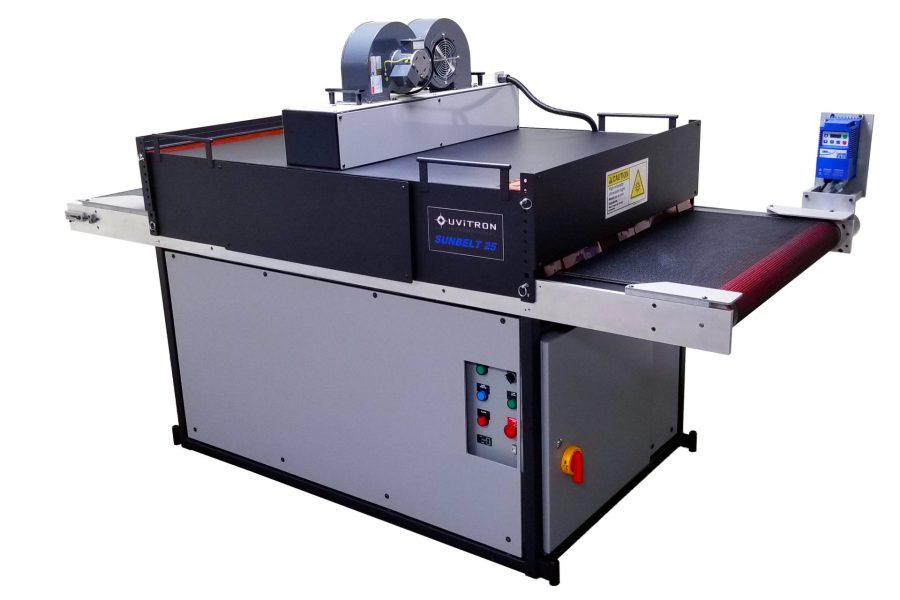
Sunbelt 25 UV Conveyor
The Uvitron SunBelt 25, with its wide-width and high-power light-curing capabilities, is perfectly suited to meet the increasing demands of the printed electronics industry. Its unique features make it an ideal solution for various applications in this sector, providing efficient and reliable UV curing for high volume production or large parts processing in laboratory settings.
Printed Circuit Boards (PCBs): The Uvitron SunBelt 25’s high-output arc lamp and programmable electronic power regulating ballast ensure precise, consistent curing of photosensitive materials used in PCB manufacturing. Its wide conveyor belt can accommodate large PCBs or multiple smaller boards, significantly increasing throughput and productivity. In addition, the SunBelt 25 can also be used to secure electronic components to PC board assemblies using UV adhesives, and to seal portions of the assemblies using UV cured form-in-place gaskets. The SunBelt 25 can also encapsulate small PC boards in UV cured potting compounds for shock and vibration protection or to prevent tampering or reverse engineering of sensitive board designs.
Flexible Electronics: The variable-speed motor and velocity regulating drive of the SunBelt 25 allow for precise control over curing times, ensuring that flexible substrates are not damaged or warped during the curing process. This is particularly important when manufacturing flexible electronic components such as wearable devices, sensors, or displays.
Large-Scale Printed Sensors: The SunBelt 25’s long, enclosed UV curing tunnel enables the efficient production of large-scale printed sensors or multiple smaller sensors simultaneously. Its entrance and exit light guards provide maximum light shielding, ensuring uniform curing and reducing the risk of overexposure or underexposure.
Displays and Lighting: The Uvitron SunBelt 25 can be utilized to cure organic layers in displays and lighting applications, providing a reliable and efficient solution for manufacturing these products. Its precise curing capabilities help to ensure optimal performance, stability, and longevity of the final product.
Research and Development: Laboratories working on the development of new materials, processes, or applications in printed electronics can benefit from the SunBelt 25’s precise curing control, wide conveyor belt, and high-output arc lamp. This system allows researchers to effectively test and optimize curing parameters for various materials and substrates, accelerating the development of innovative solutions in the printed electronics sector.
In conclusion, the Uvitron SunBelt 25 is a versatile UV curing system that can significantly enhance the manufacturing and development of printed electronics. Its unique features, such as the high-output arc lamp, wide conveyor belt, and precise curing control, make it a valuable tool for various applications within the industry, ultimately contributing to improved efficiency, productivity, and innovation.