May 30, 2023 | Blog
UV-LED curing stands at the forefront of curing technology, utilizing ultraviolet light-emitting diodes (UV-LEDs) to activate a reaction in photosensitive materials, causing them to harden or ‘cure’. From the realms of inkjet printing to adhesive bonding, coating application, and beyond, this revolutionary process is finding its foothold in diverse industrial applications. Diverging from the traditional path, UV-LED curing replaces conventional mercury-based UV lamps with UV-LED lights, presenting a host of compelling benefits. This paradigm shift has not only introduced a more efficient, safe, and environmentally conscious solution to the industry but also has been instrumental in overcoming various operational challenges typically associated with traditional UV curing.
The Mechanics of UV-LED Curing
The core of UV-LED curing technology lies in its innovative use of ultraviolet light. The system uses specially designed LED lights that emit ultraviolet light at specific wavelengths. These wavelengths, typically in the UVA range (320-400nm), are carefully chosen to align with the absorption peak of the photoinitiators present in the photosensitive materials.
When these materials are exposed to UV light from the LEDs, the photoinitiators within them become excited, and a chemical reaction is triggered. This reaction prompts the polymers in the material to link together, forming a three-dimensional cross-linked network. The result is a rapid transformation from a liquid or semi-liquid state to a hardened or ‘cured’ state, without the need for additional solvents or drying time.
UV-LED Curing Vs. Conventional UV Curing
The adoption of UV-LED curing over traditional mercury-vapor UV lamps heralds a sea change in the industrial landscape. Notably, UV-LED curing mitigates several inherent challenges posed by mercury-based UV lamps. Firstly, UV-LED curing is significantly more energy-efficient than its predecessor. The technology requires less power to operate, reducing energy consumption, and consequently, operational costs. Secondly, UV-LED curing is safer for both operators and the environment. Traditional mercury UV lamps generate a significant amount of heat and emit potentially harmful UV-C and UV-B radiation. Conversely, UV-LED lights produce minimal heat and emit light only in the safer UVA range, thereby diminishing the risk to operators. Also, the absence of mercury in UV-LEDs eliminates the need for hazardous waste disposal. Finally, UV-LED curing contributes to a more sustainable industrial landscape. The longer life cycle of UV-LED lights, combined with their lower energy consumption, results in a smaller carbon footprint. Moreover, UV-LED curing facilitates cleaner processes, as it allows for solvent-free formulations, promoting a healthier working environment and less pollution.
The Benefits of UV-LED Curing
Superior Energy Efficiency
UV-LEDs operate with substantially lower energy consumption compared to traditional mercury UV lamps. This higher efficiency is primarily due to the instant on-off capability of UV-LEDs, reducing energy wastage during idle periods. Additionally, UV-LEDs emit light at the exact wavelengths required for curing, eliminating the need for energy-consuming filters required in traditional systems. The result is not only a significant reduction in power usage, but also lower utility bills, making UV-LED curing a cost-effective choice for industries.
Eco-Friendly Operation
UV-LED curing technology is a poster child for green industrial operations. Unlike mercury-based lamps, UV-LEDs do not contain any mercury, a harmful pollutant. Traditional lamps require careful disposal to prevent mercury from harming the environment. By contrast, the mercury-free nature of UV-LEDs means no special disposal procedures, reducing the environmental footprint of the curing process. Also, UV-LED curing often enables formulations without volatile organic compounds (VOCs), reducing air pollution and contributing to a cleaner, safer workplace.
Decreased Heat Output
One of the key advantages of UV-LED curing is its significantly lower operating temperature compared to conventional UV lamps. This reduced heat output offers several benefits. Firstly, it expands the range of materials that can be cured, including heat-sensitive substrates that may deform or discolour under traditional UV lamps. This opens up new possibilities for industries such as electronics and medical devices, where heat-sensitive components are commonplace. Secondly, the low heat output enhances worker safety by minimizing the risk of accidental burns during operation.
Longer Lifespan
A typical UV-LED light source is estimated to have an operational life of around 20,000 hours or more, a significant leap from the average 1,000 to 2,000 hours offered by conventional mercury UV lamps. The extensive lifespan of UV-LEDs comes from their fundamentally different method of generating UV light. Rather than relying on an excited mercury vapor, UV-LEDs use semiconductor materials to create light. These materials are much more durable and do not degrade over time to the same degree as the elements in a mercury UV lamp. This longevity directly leads to several operational advantages.
Instant On/Off
Traditional mercury lamps require a substantial amount of time to warm up and achieve the necessary intensity for effective curing. This limitation not only consumes time but also restricts operational flexibility. Conversely, UV-LEDs offer an immediate response. They reach their full intensity within microseconds, eliminating any wait time. This responsiveness is particularly advantageous in production environments that require frequent start-stop cycles, enabling instant curing whenever needed.
Greater Process Control
In a UV-LED system, operators can easily adjust the intensity of the emitted light. This is a significant advantage over traditional mercury lamps, which usually operate at a fixed intensity. The ability to modify light intensity grants operators the flexibility to fine-tune the curing process based on the specific requirements of the materials and applications at hand. For example, sensitive materials may require lower intensity to prevent damage, while other materials may necessitate higher intensity for a robust cure.
Uvitron International: Our UV-LED Curing Systems
SkyRay
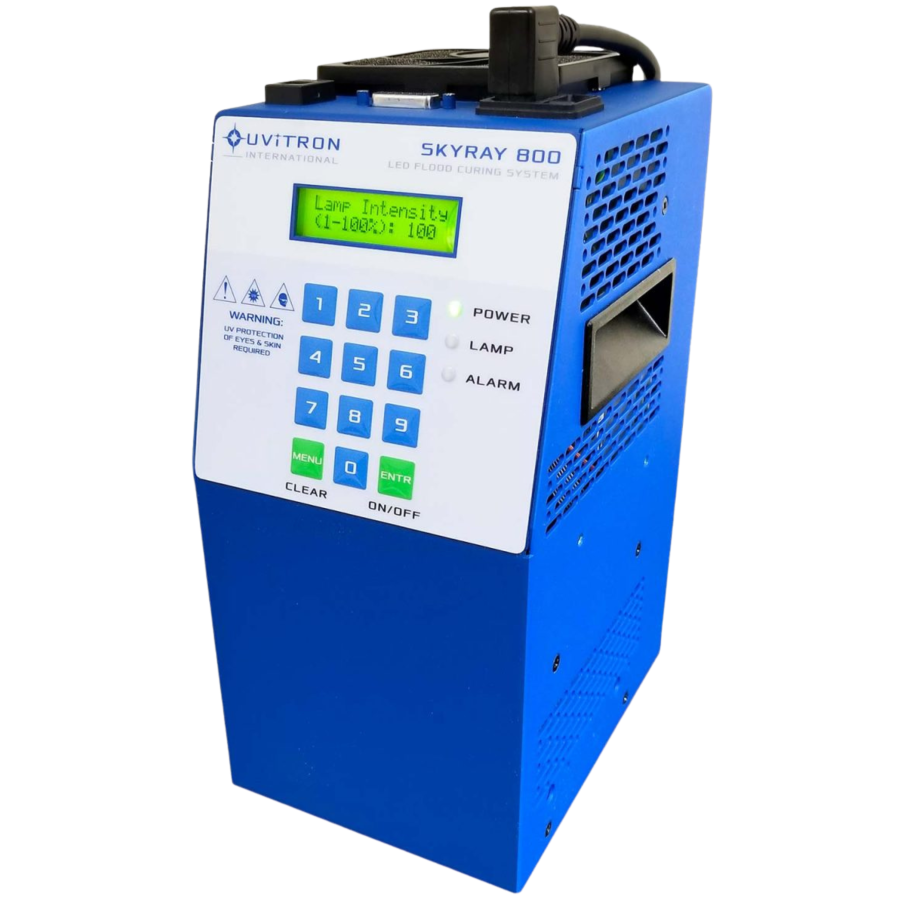
Uvitron International’s SkyRay UV-LED curing system exemplifies the technological advancements driving the curing industry. Boasting a compact, integrated design, this high-performance device brings remarkable efficiency and control to the curing process. The SkyRay system elegantly integrates all necessary components into a small lamp head, rendering the need for remote controllers, power supply boxes, or remote coolers obsolete. Its ease of installation—simply mount the head, connect the AC power cord, and begin—makes it a versatile addition to any factory floor. This potent device illuminates a 5 x 5-inch curing area with cool, high-intensity light evenly distributed across the area, courtesy of long-life, solid-state LEDs. The system offers adjustable output intensity, accommodating the curing needs of different materials. SkyRay features a built-in exposure timer and an intuitive front panel LCD display, making programming and monitoring of curing operations straightforward. It ensures process integrity through password protection, preventing unauthorized changes to sensitive processes and control settings. A variable-speed cooling fan ensures optimal operating conditions, while the slim enclosure design, complete with flush-mounted carrying handles, allows for side-by-side mounting of multiple units. This makes it possible to cure larger areas simultaneously.
SkyBeam
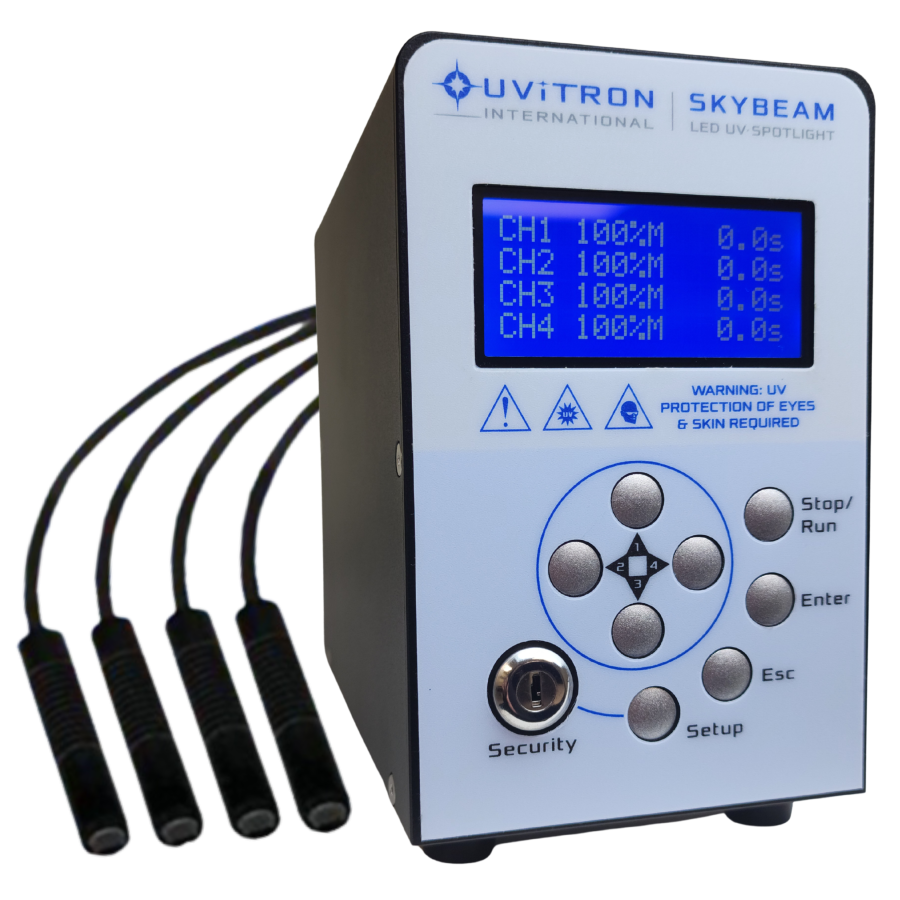
The SkyBeam LED spotlight curing system is a high-intensity, cool-operation curing solution that has earned its reputation in both benchtop and automated production lines. Weighing a mere 3.25 lbs., this compact unit blends power with ease of use and is designed to handle demanding industrial environments. The SkyBeam system supports up to four independently operating light guides, each offering a 0–999.9 second exposure timer and a 10–100% power adjustment range. It includes a long-life light guide, with the flexibility to adjust the UV light spot size by replacing the optical lens at the end of each guide. This capability ensures tailored irradiation, enhancing the curing process for a variety of applications.
May 22, 2023 | Blog
Ultraviolet (UV) curing technology is making waves across a multitude of industries, offering a cutting-edge solution for curing and solidifying inks, coatings, and adhesives. By harnessing the power of UV light, businesses are unlocking new opportunities for cost savings, streamlined processes, and enhanced efficiency. As the market continues to evolve and competition intensifies, adopting UV curing technology is becoming increasingly crucial for businesses aiming to reduce expenses and stay ahead of the curve.
Accelerated Production Times: A Key Advantage of UV Curing
A standout advantage of UV curing technology is its impressive ability to slash production times significantly. Traditional methods such as air drying or thermal curing often require hours to achieve the desired results, which can lead to bottlenecks in the production process. In contrast, UV curing technology streamlines this process by curing materials in just a matter of seconds, resulting in a more efficient workflow.
The substantial reduction in curing time afforded by UV technology enables businesses to ramp up their production rates, allowing them to complete more projects within the same timeframe. This increased efficiency not only translates to cost savings but also gives businesses a competitive edge in fast-paced markets. By adopting UV curing technology, companies can cater to higher demand, respond more quickly to market changes, and capitalize on opportunities for growth.
Furthermore, the accelerated production times offered by UV curing technology can lead to a more agile and responsive supply chain. By reducing lead times and minimizing the risk of production delays, businesses can better meet the needs of their customers, enhancing overall customer satisfaction and fostering long-lasting relationships.
Minimized Energy Consumption: The Eco-Friendly Benefit of UV Curing
UV curing technology stands out as an energy-efficient alternative to traditional curing methods, presenting businesses with an opportunity to save on energy costs and contribute to a greener planet. Conventional thermal curing techniques demand substantial energy inputs to maintain the high temperatures necessary for the curing process. In contrast, UV curing systems harness the power of focused UV light to initiate curing, requiring considerably less energy in the process.
By adopting UV curing technology, businesses can significantly reduce their energy consumption, resulting in lower energy bills and long-term savings. This reduction in energy use not only benefits the bottom line but also helps companies minimize their carbon footprint and demonstrate a commitment to sustainability. In an era where consumers are becoming increasingly environmentally conscious, adopting eco-friendly practices can also enhance brand reputation and customer loyalty.
Furthermore, the energy-efficient nature of UV curing technology can help businesses comply with regulatory requirements and industry standards related to energy consumption and emissions. By proactively addressing these concerns, companies can avoid potential fines and penalties while staying ahead of the curve in an increasingly regulated business landscape.
Minimizing Waste and Rejects: Enhancing Quality with UV Curing Technology
UV curing technology offers the distinct advantage of reducing production defects and rejects, leading to higher-quality products and increased cost savings for businesses. The rapid curing process facilitated by this technology ensures that materials are cured uniformly and consistently, which significantly decreases the likelihood of imperfections. As a result, businesses can maintain a higher standard of quality, which in turn can bolster customer satisfaction and brand reputation.
Moreover, the precision of UV curing systems contributes to a decrease in material waste during the production process. By using only the required amount of inks, coatings, or adhesives, businesses can minimize waste and achieve more efficient use of resources. This precision not only leads to cost savings by reducing material expenditures but also promotes a more sustainable and eco-friendly production process.
The reduction in waste and rejects also has a positive ripple effect on other areas of business operations. For instance, with fewer defects and returns, businesses can save on costs associated with handling and disposing of rejected products, as well as the expenses related to processing customer returns and exchanges. Additionally, a decrease in production rejects can result in more accurate inventory management, enabling businesses to optimize their storage space and streamline their supply chain.
Reduced Maintenance Costs: The Efficiency Advantage of UV Curing Systems
UV curing systems offer the valuable benefit of lower maintenance costs compared to traditional curing equipment. With fewer moving parts, these systems are less prone to mechanical wear and tear, resulting in increased durability and a longer lifespan. Additionally, the absence of heating elements and cooling systems in UV curing equipment eliminates the need for regular cleaning and maintenance associated with these components.
This reduction in maintenance requirements translates to significant cost savings for businesses. By spending less on maintenance and repair, companies can allocate those resources to other areas of their operations, such as research and development, marketing, or employee training. Furthermore, the time saved on maintenance tasks can be used to focus on more productive activities, ultimately contributing to overall business efficiency and growth.
Besides cost savings, lower maintenance requirements also offer the benefit of reduced downtime in production. With traditional curing equipment, production can be disrupted by the need for regular maintenance, cleaning, or repairs. UV curing systems, on the other hand, minimize such disruptions, ensuring a more reliable and continuous production process. This increased reliability can lead to improved customer satisfaction, as businesses can better meet deadlines and maintain consistent product quality.
Promoting a Safer Work Environment: The Health and Safety Benefit of UV Curing Technology
One of the most significant advantages of UV curing technology is its ability to create a safer work environment, which in turn can reduce associated costs and protect your employees. Traditional curing methods often require high heat and the use of hazardous chemicals, posing risks to workers and potentially leading to accidents or health issues. In contrast, UV curing systems operate without generating excessive heat and rely on more environmentally friendly materials, minimizing potential hazards.
By implementing UV curing technology, businesses can decrease the likelihood of workplace accidents, which not only helps protect their most valuable asset—their employees—but also results in cost savings. Fewer accidents mean lower workers’ compensation claims, reduced lost workdays, and decreased insurance costs. Additionally, fostering a safe work environment can contribute to increased employee satisfaction and retention, reducing the costs associated with turnover and recruitment.
Creating a safer work environment also has positive implications for a company’s reputation. By demonstrating a commitment to employee health and safety, businesses can enhance their brand image and appeal to both customers and potential employees who prioritize responsible practices. This positive brand perception can lead to increased customer loyalty and help attract top talent in the industry.
Uvitron International: Driving the UV Curing Technology Revolution
At Uvitron International, we are proud to be at the forefront of the UV curing technology revolution. As a US-based manufacturer specializing in the design and production of UV curing systems, we have harnessed the power of UV light to provide cutting-edge solutions for curing and solidifying inks, coatings, and adhesives. We are dedicated to innovation, and our commitment to quality has established us as a leader in our field.
In a rapidly evolving market with growing competition, we recognize the importance of providing businesses with the tools they need to optimize their processes and reduce expenses. With this in mind, we have developed our UV curing technology to offer a multitude of benefits that can drive operational efficiency and provide significant cost savings.
Our UV curing systems are designed to streamline the curing process, drastically reducing production times compared to traditional methods. The speed and efficiency of our technology can transform workflows, eliminating bottlenecks and enhancing productivity. The result? Businesses can complete more projects within the same timeframe, cater to higher demand, and seize opportunities for growth.
But our commitment to driving efficiency doesn’t stop there. At Uvitron, we’re passionate about sustainability and continuously strive to minimize our impact on the environment. We’ve designed our UV curing technology to be an energy-efficient alternative to traditional curing methods, enabling businesses to reduce their energy consumption and contribute to a greener planet.
Through the use of our UV curing systems, businesses can not only lower their energy bills and make long-term savings, but they can also demonstrate their commitment to sustainable practices. We believe that in an era where consumers are increasingly environmentally conscious, this is a powerful way to enhance brand reputation and customer loyalty.
Our technology also plays a critical role in enhancing the quality of products. The precision and consistency of our UV curing systems significantly reduce the likelihood of production defects and rejects, ensuring materials are cured uniformly. The result is a higher standard of quality that bolsters customer satisfaction and reinforces brand reputation.
Furthermore, our UV curing systems offer the advantage of lower maintenance costs. Designed with fewer moving parts and without the need for heating elements or cooling systems, our equipment is less prone to mechanical wear and tear. This reduction in maintenance translates to significant cost savings and contributes to the overall business efficiency and growth.
Lastly, safety is a core priority at Uvitron. We have developed our UV curing systems to create a safer work environment, minimizing potential hazards associated with traditional curing methods that often require high heat and the use of hazardous chemicals. By implementing our UV curing technology, businesses can protect their most valuable asset—their employees—while reducing associated costs and enhancing their reputation for responsible practices.
At Uvitron International, we’re not just providing technology—we’re driving change. We’re empowering businesses to meet the demands of today’s market and paving the way for a more efficient, sustainable, and safe future. We’re excited to continue innovating and helping businesses stay ahead of the curve in the world of UV curing technology.
May 15, 2023 | Blog
As we push the boundaries of the 21st century, the importance of the aerospace and defense industries cannot be understated. These sectors are vital to national security, global communication, scientific discovery, and the burgeoning space tourism industry. However, as our reliance on these industries intensifies, so does the demand for materials that can endure high-stress environments and extreme conditions, all while maintaining optimal performance.
Enter Ultraviolet (UV) light curing technology. This innovative technique, which employs UV light to rapidly cure or harden materials, emerges as a potential linchpin in the evolution of aerospace and defense sectors. It offers a promising solution to the ever-growing need for materials that are not only resilient but also efficient to produce and apply.
In the high-stakes world of aerospace and defense, reliability is paramount. Equipment must perform flawlessly under extreme conditions, from the heat and radiation of space travel to the pressures of deep-sea operations. UV light curing systems have proven to be remarkably reliable in these challenging environments.
UV-cured materials possess the extraordinary durability necessary for such demanding applications. They are resistant to extreme temperatures, radiation, and mechanical stresses, making them particularly suited to the rigorous demands of aerospace and defense. Furthermore, the rapid curing process reduces the risk of contaminants being trapped within the material, leading to a more robust and reliable end product.
Accelerating Innovation: The Rapid-On-Demand Curing of UV Technology
One of the standout qualities of UV curing technology is its remarkable ability to provide rapid, on-demand curing. This is not just a mere convenience but a significant game-changer, particularly in sectors such as aerospace, where timelines are tight, and the demand for high-performance materials is relentless.
In aerospace manufacturing, time is of the essence. The industry is marked by its need for materials that can withstand extreme conditions — from the intense heat and radiation of a rocket launch to the cold vacuum of space. In this high-stakes landscape, the accelerated curing time offered by UV light technology is not just a luxury; it’s a necessity.
UV curing technology can harden materials in mere seconds or minutes, a stark contrast to the hours or even days required by traditional curing methods. This rapid-curing feature significantly accelerates production cycles, allowing aerospace manufacturers to produce more components in less time. This has a ripple effect on efficiency, allowing for quicker assembly, reduced lead times, and faster delivery of the final product to clients or missions.
Furthermore, the swift curing process drastically reduces work-in-progress inventory. This is crucial in an industry where space optimization is paramount. Less time spent waiting for materials to cure means fewer components taking up valuable space on the production floor. The result is a leaner, more efficient manufacturing environment that can better adapt to fluctuating demand and tight deadlines.
Unyielding Endurance: The Role of UV-Cured Materials in Defense Applications
In the demanding realm of defense applications, materials are expected to endure the harshest of conditions, whether it’s the scorching heat of desert deployments or the bone-chilling cold of polar missions. The durability and environmental resistance of UV-cured materials make them a particularly attractive option for these high-stress situations.
UV-cured materials are engineered to be extraordinarily durable, designed to withstand significant mechanical stresses without damage or degradation. This is a vital attribute in defense applications, where materials must endure everything from high-impact shocks and vibrations to corrosive elements and wear-and-tear.
The standout feature of these materials is their inherent resistance to environmental degradation. UV-cured materials are less susceptible to the harmful effects of sunlight, moisture, and extreme temperatures, making them ideal for use in outdoor and challenging environments common in defense scenarios.
Consider the varying climates where defense operations take place. In the scorching heat of desert deployments, materials are exposed to extreme temperatures and intense UV radiation. Conversely, during polar missions, they must withstand frigid temperatures and potential ice formation. UV-cured materials maintain their structural integrity and performance under these extremes, a testament to their robustness.
Another crucial factor to consider is the corrosive nature of saltwater in naval defense applications. UV-cured materials exhibit exceptional resistance to this corrosive element, ensuring that naval vessels and equipment can maintain peak operational readiness even in the harsh conditions of the open sea.
In a field where failure is not an option, the durability and resistance of UV-cured materials to environmental degradation offer invaluable reliability. From the heat of the desert to the cold of the poles, UV-cured materials are proving their worth in defense applications, providing confidence in the face of adversity and uncertainty. Their ability to withstand the rigors of service in the most challenging conditions marks them as a critical component in the future of defense technology.
Lightening the Load: The Impact of UV-Cured Composites on Aerospace Sustainability
One of the most transformative applications of UV curing technology lies in the creation of lightweight composites. This is particularly game-changing for the aerospace industry, where every ounce counts. By replacing traditionally heavy materials with UV-cured composites, the industry can achieve significant weight reduction, leading to a host of benefits, from improved fuel efficiency to reduced carbon emissions.
The weight of an aircraft has direct implications on its fuel consumption. The lighter the aircraft, the less fuel it requires to maintain flight. By employing UV-cured composites in place of heavier materials, aerospace manufacturers can build lighter aircraft without compromising on strength or durability. This leads to a noticeable improvement in fuel efficiency, an essential factor in an era of rising fuel costs and increasing environmental consciousness.
Reduced fuel consumption also translates to lower carbon emissions. As the global community becomes more aware of the urgent need to mitigate climate change, industries worldwide are being called upon to reduce their environmental footprints. The aerospace industry is no exception. By adopting UV-cured composites and thereby reducing fuel consumption, the industry can significantly lower its greenhouse gas emissions, aligning with global sustainability goals.
Moreover, UV-cured composites have the potential to increase the lifespan of aircraft components. These materials are resistant to wear and tear, corrosion, and environmental degradation, which means they last longer than many traditional materials. Longer-lasting components mean fewer replacements, less waste, and lower resource consumption over the lifetime of an aircraft.
Cutting Costs and Time: The Maintenance Advantage of UV-Cured Coatings
The benefits of UV curing technology extend well beyond the manufacturing process, offering substantial advantages in the maintenance phase as well. Specifically, UV-cured coatings have proven to demonstrate exceptional durability and longevity, leading to reduced maintenance time, lowered costs, and enhanced operational readiness in both aerospace and defense applications.
UV-cured coatings exhibit superior resistance to wear and tear, corrosion, and environmental degradation. This durability ensures that the coated components require fewer touch-ups and replacements over their operational life, significantly reducing the time spent on maintenance activities. In industries where downtime can cost millions, the time saved by using UV-cured coatings can translate into substantial financial savings.
Cost reduction is another significant benefit of UV-cured coatings. Traditional coatings often require frequent reapplication due to wear and degradation, leading to high material and labor costs. In contrast, the superior durability of UV-cured coatings means they need to be replaced less frequently, thus saving on the cost of materials and the labor involved in reapplication.
Moreover, these coatings cure almost instantly under UV light, as opposed to traditional coatings that may require several hours or even days to cure fully. This accelerated curing process further reduces downtime, allowing equipment to return to service quickly and thus maintaining high operational readiness.
In the case of defense applications, the ability to rapidly cure coatings could even have tactical advantages. Equipment can be repaired and returned to service quickly, potentially making a significant difference in mission-critical situations.
The potential of UV curing technology to reduce maintenance time and costs signifies yet another way this innovation is transforming the aerospace and defense industries. By enhancing durability, reducing downtime, and lowering maintenance costs, UV-cured coatings promise to contribute significantly to the efficiency and effectiveness of these crucial sectors.
Safety and Sustainability: The Health and Environmental Benefits of UV Curing
The integration of UV curing technology into aerospace and defense material technologies doesn’t just enhance efficiency and performance; it also fosters safer, healthier work environments. Unlike conventional curing methods that often involve toxic solvents, UV curing is a solvent-free process. This has significant implications for workforce health and safety, as well as for broader sustainability goals within the industry.
Traditional curing methods often require the use of solvents that can release hazardous volatile organic compounds (VOCs) into the atmosphere during the curing process. Workers exposed to high levels of these compounds may experience health issues, including headaches, dizziness, skin irritation, and in severe cases, damage to the liver, kidneys, or central nervous system.
By contrast, UV curing technology eliminates the need for these harmful solvents. The process uses UV light to cure materials, resulting in a significant reduction in VOC emissions. This mitigates the risk of health issues associated with VOC exposure, providing a safer and healthier working environment for employees in the aerospace and defense industries.
Moreover, the reduction in VOC emissions also contributes to the industry’s environmental sustainability goals. VOCs are known contributors to air pollution, including the formation of ground-level ozone, a key component of smog. By reducing VOC emissions, UV curing technology helps to lessen the industry’s environmental impact, aligning with global efforts to combat air pollution and climate change.
Uvitron International: Empowering Aerospace and Defense with Advanced UV Curing Solutions
Since 1993, Uvitron International has grown into a comprehensive provider of light-curing systems, UV power supplies, and UV curing accessories. Today, our innovative UV curing solutions are actively utilized by defense contractors and armed forces, playing a pivotal role in the aerospace and defense sectors.
Our primary mission is to enhance the capabilities of these critical sectors by providing cutting-edge UV curing technology. Uvitron’s UV curing systems facilitate rapid, on-demand curing, which is a game-changer for defense contractors and armed forces operating under tight timelines and high-stakes conditions. The accelerated production cycles and improved efficiency driven by our systems have become invaluable in these demanding environments.
Uvitron International’s commitment to quality and performance is reflected in our reputation for manufacturing superior products. Our systems are made in the USA and backed by a wealth of product knowledge and in-house expertise. Our aim is to deliver affordably priced UV curing solutions.
Our dynamic and support-oriented company is distinguished by an experienced team of engineers, programmers, technicians, and professional sales executives who provide our customers with exceptional expertise. With all electrical, optical, and mechanical design of our products performed in-house, we are able to share comprehensive technical knowledge with our customers.
Additionally, Uvitron offers custom-designed light-curing systems, along with systems consulting, design, and manufacturing services. Our aim is not just to provide solutions, but to drive innovation in the aerospace and defense sectors, equipping our customers with technology that helps them stay at the forefront of their fields. Uvitron International is more than a solutions provider – we are a partner in progress, dedicated to powering the success of our clients in the aerospace and defense industries.
May 2, 2023 | Blog
In an era defined by rapid technological advancements, the medical field has seen a significant development: the integration of UV light curing systems. This cutting-edge technology is transforming multiple aspects of healthcare, but two areas are seeing particularly impressive impacts – the manufacturing of surgical tools and the creation of prosthetics.
Prosthetics and Implants: A Perfect Fit
As advancements in the medical field continue to accelerate, the focus on personalized care and treatment is at an all-time high. One of the most notable areas where this trend is evident is in the creation of prosthetics and implants. Customization is crucial for these medical aids, as they need to fit perfectly and work seamlessly with the body for optimal functionality, comfort, and patient satisfaction.
This is where UV light curing systems come into play, bringing a level of precision and efficiency that is transforming the field. These systems, when combined with 3D printing technology, are enabling the creation of patient-specific prosthetics and implants with unprecedented accuracy. UV-curable materials can be precisely shaped and rapidly cured to fit the unique physical characteristics of each patient. This leap forward in personalization ensures that each prosthetic or implant is tailor-made to provide the best possible fit and performance.
The UV light curing process offers significant advantages over traditional production methods. The rapid curing times of UV-curable materials dramatically reduce production times, making it possible to efficiently create custom-fit prosthetics and implants. This is particularly beneficial in high-demand situations or when patients require immediate treatment.
Beyond speed, UV-curable materials also offer superior biocompatibility and low toxicity. When it comes to prosthetics and implants, which are often in long-term contact with the human body, these characteristics are paramount. UV-curable materials ensure that these essential medical aids not only fit perfectly but are also safe for prolonged use. This reduces the risk of adverse reactions and complications, leading to better overall patient outcomes.
Moreover, the flexibility of UV-curable materials means they can be used to create a wide range of prosthetics and implants, from simple devices to complex bioengineered structures. This versatility, combined with the customization capabilities of 3D printing, opens up a world of possibilities for patient-specific treatments.
As UV light curing systems become more integrated into the production of prosthetics and implants, their benefits are becoming increasingly evident. By enabling high levels of precision, efficiency, and safety, these systems are playing a pivotal role in advancing personalized medicine, ultimately leading to improved patient care, better outcomes, and enhanced quality of life.
With ongoing advancements and research, the potential for UV light curing systems in the field of prosthetics and implants is vast. As we continue to explore and harness the power of this cutting-edge technology, its transformative impact on healthcare is set to continue to evolve and expand.
Redefining the Production of Surgical Tools
In the rapidly evolving medical industry, UV light curing systems have emerged as a pivotal technological advancement, particularly in the production of surgical tools. These innovative systems are not only enhancing the functionality of surgical instruments but also revolutionizing the production processes.
UV-curable coatings, in particular, are transforming the performance parameters of critical surgical instruments such as catheters and endoscopes. These coatings significantly augment the lubricity of surgical tools, thereby mitigating friction during invasive procedures. This enhancement enables smoother insertion and superior navigability of these tools, facilitating precise and efficient surgical interventions. This is an invaluable benefit, especially in complex procedures where surgical dexterity can dramatically affect patient outcomes.
Moreover, UV light curing systems have become instrumental in optimizing the production cycle of these surgical tools. The use of UV-curable materials leads to expeditious curing times, a critical advantage in a sector where time-efficiency is synonymous with cost-effectiveness. Furthermore, UV-curable coatings are reputed for their durability and resilience against environmental stressors such as humidity and temperature fluctuations. This feature ensures the sustained performance and longevity of the surgical tools, offering a reliable solution for maintaining high surgical standards over time.
The versatility of UV-curable materials further expands their application scope in the production of an array of surgical tools. From rudimentary devices to sophisticated bioengineered instruments, UV light curing systems are equipped to address a broad spectrum of surgical requirements. This versatility, when coupled with the rapid curing process, cements the position of UV light curing systems as a transformative force in the surgical tools manufacturing sector.
Uvitron International: A Company Built on Innovation and Expertise
Uvitron International was established in 1993, initially as a developer and manufacturer of switch-mode power supplies for light curing systems. When the company developed their first electronic arc lamp power supply, it marked the beginning of an ongoing commitment to innovation and quality. Over the years, Uvitron has expanded its scope, evolving into a total solutions provider for UV light curing systems, UV power supplies, and UV curing accessories. Made in the USA and supported by extensive product knowledge and in-house expertise, Uvitron has earned a reputation for manufacturing and selling superior quality products. The company strives to produce affordably priced UV curing solutions that offer equal or better performance than other products in the market. Uvitron distinguishes itself as a dynamic and support-oriented company. Its experienced staff, consisting of engineers, programmers, technicians, and professional sales executives, provides customers with a high degree of expertise. By performing all electrical, optical, and mechanical design in-house, the company ensures comprehensive technical knowledge is readily available to customers.
Apr 27, 2023 | Blog
The popularity of UV curing adhesives has been steadily growing across various industries, primarily due to their numerous benefits, such as rapid curing times, outstanding bonding capabilities, and environmentally friendly characteristics. These adhesives have proven to be a game-changer, offering a significant edge over traditional bonding methods and making them the preferred choice for a wide range of applications.
Choosing the perfect adhesive and curing system for your specific application is of paramount importance to ensure optimal results, long-lasting performance, and overall efficiency. In order to help you make an informed decision, we have compiled an extensive guide that will explore the critical factors you need to consider when selecting a UV curing adhesive and the appropriate UV light system.
Substrate Compatibility
When it comes to selecting a UV curing adhesive, substrate compatibility plays a vital role in ensuring a successful bonding process.
Identifying the Materials: When selecting a UV curing adhesive, one of the primary factors to consider is substrate compatibility. This refers to the ability of the adhesive to bond effectively with the materials in your specific application. Ensuring compatibility between the adhesive and substrates is crucial for creating a strong, durable bond that can withstand the demands of its intended use. To determine substrate compatibility, start by identifying the materials you will be bonding together. Common substrates include metals, plastics, glass, ceramics, and composites. It is important to note that different materials have distinct surface properties that can affect the adhesive’s ability to bond effectively. For example, low surface energy plastics, such as polyethylene and polypropylene, can be more challenging to bond compared to high surface energy materials, like metals or glass.
Consulting Manufacturer’s Recommendations: Once you have identified the substrates involved, consult the manufacturer’s recommendations for compatible materials. UV curing adhesive manufacturers typically provide technical data sheets or product guides that list the substrates their adhesives are designed to bond. These resources can be invaluable in helping you narrow down your adhesive options and find one that is well-suited for your specific materials.
Surface Preparation and Primer Application: In some cases, surface preparation or the use of primers may be necessary to enhance the bond between the adhesive and substrate. Proper surface preparation can include cleaning, roughening, or applying a primer to improve the adhesive’s ability to bond to the material. Always follow the manufacturer’s guidelines for surface preparation and primer application to achieve the best possible results.
Bonding Requirements
Understanding the bonding requirements of your specific application is another crucial factor when selecting a UV curing adhesive. The adhesive you choose should possess the appropriate strength and flexibility characteristics to ensure the bonded assembly performs as intended.
Tensile and Shear Strength: The tensile strength of an adhesive refers to its ability to withstand forces that pull the bonded materials apart, while shear strength refers to its resistance against forces that cause the materials to slide against each other. Applications involving heavy loads, high stress, or structural bonding typically demand adhesives with high tensile and shear strength. Carefully review the technical data sheets provided by adhesive manufacturers to find a product with the necessary strength properties for your application.
Flexibility and Elongation: Flexibility is the adhesive’s ability to bend or flex without breaking, whereas elongation is the extent to which it can be stretched before breaking. Some applications may require adhesives with greater flexibility and elongation to accommodate movement, thermal expansion, or stress relief. For example, bonding materials with different coefficients of thermal expansion or applications subject to vibrations may benefit from a more flexible adhesive. Look for products with the appropriate flexibility and elongation characteristics in the manufacturer’s technical data.
Impact Resistance: In some applications, the bonded assembly may be exposed to impact forces or sudden shocks. In such cases, it is essential to choose an adhesive with high impact resistance to prevent bond failure or damage to the assembly. Adhesives with higher impact resistance are generally more resilient and can better absorb and distribute impact forces, ensuring the bonded materials remain intact even under challenging conditions. Check the manufacturer’s technical data sheets for information on the adhesive’s impact resistance properties.
Cure speed is an essential factor to consider when selecting UV curing adhesives, as it directly impacts your production speed and overall efficiency. UV curing adhesives can offer varying cure speeds depending on their formulation and the intensity of the UV light source used. To ensure a smooth production process and meet your specific requirements, it’s crucial to choose an adhesive with an appropriate cure time.
Formulation and UV Light Intensity: The cure speed of a UV curing adhesive is influenced by its chemical formulation and the intensity of the UV light source. Adhesives with highly reactive formulations tend to cure more rapidly, while those with less reactive components may require longer exposure to UV light. The intensity of the UV light source also plays a significant role in determining cure speed, with higher intensities leading to faster curing times.
Production Speed and Process Requirements: Consider your production speed and process requirements when selecting an adhesive with the right cure speed. High-volume production lines or processes that demand rapid assembly may benefit from adhesives with faster cure times. On the other hand, applications that involve complex assemblies or require precise positioning of parts may benefit from adhesives with slower cure speeds, providing more time for adjustments before the adhesive sets.
Balancing Cure Speed and Performance: It’s essential to strike a balance between cure speed and adhesive performance. While faster cure times can boost production efficiency, they may sometimes compromise the adhesive’s overall performance, such as bond strength or flexibility. Therefore, it’s crucial to select an adhesive that offers the optimal cure speed without sacrificing the performance characteristics required for your specific application.
Viscosity
Another critical aspect to consider when choosing a UV curing adhesive is the viscosity of the adhesive. The appropriate viscosity depends on the specific requirements of your application.
Low-Viscosity Adhesives: Low-viscosity adhesives are ideal for applications requiring thin bond lines or capillary action. These adhesives can easily flow into tight spaces and create a strong bond between closely-fitting parts. Low-viscosity adhesives are often used in applications such as bonding glass or optical components, where a thin and uniform bond line is crucial.
Medium-Viscosity Adhesives: Medium-viscosity adhesives offer a balance between flowability and gap-filling capabilities. They can be used in a wide range of applications, providing versatility for various bonding requirements. This type of adhesive is suitable for applications that need a moderate bond line thickness or a combination of capillary action and gap filling.
High-Viscosity Adhesives: High-viscosity adhesives are better suited for gap filling or vertical applications where a thicker bond line is needed or where the adhesive must remain in place without sagging or flowing. These adhesives are typically used in applications that require more robust bonding, such as structural bonding or bonding uneven or irregular surfaces.
Temperature and Chemical Resistance
When selecting a UV curing adhesive, it’s crucial to take into account the environmental conditions your bonded assembly will be exposed to. This will help ensure long-term performance and durability.
Temperature Resistance: The bonded assembly may be exposed to extreme temperatures, whether during manufacturing processes or in its end-use environment. Choose an adhesive that can withstand the temperature range your application requires. Adhesives with high-temperature resistance can maintain their bond strength and integrity under thermal stress, while those with low-temperature resistance can remain flexible and functional in cold environments.
Chemical Resistance: In some applications, the bonded assembly might come into contact with harsh chemicals, solvents, or other aggressive substances. In these cases, it is essential to select an adhesive with adequate chemical resistance to prevent bond failure or degradation. This resistance ensures the adhesive can maintain its bonding properties when exposed to the chemicals your application may encounter. Consult the adhesive manufacturer’s technical data sheets for information on chemical resistance, and consider testing the adhesive in your specific environment to verify its performance.
Dispensing Method
When selecting a UV curing adhesive, it’s essential to consider the dispensing method you plan to use, as it can impact the choice of adhesive. Some UV curing adhesives are better suited for specific dispensing methods, and selecting the right one ensures a smooth and efficient application process.
Manual Dispensing: Manual dispensing typically involves using handheld applicators, such as syringes or squeeze bottles, to apply the adhesive to the substrates. For manual dispensing, it’s important to choose an adhesive with suitable viscosity and handling properties that allow for easy application and precise control. Some adhesives may be formulated to provide longer working times or specific rheological properties, making them more suitable for manual dispensing.
Automated Dispensing Systems: Automated dispensing systems can offer increased precision, speed, and consistency in adhesive application. These systems may include robots, meter-mix equipment, or specialized applicators designed for high-volume production. When choosing an adhesive for automated dispensing, it’s crucial to select a product that is compatible with the specific equipment and parameters of your system. This may involve considering factors such as viscosity, cure speed, and pot life. Consult with the adhesive manufacturer and your dispensing equipment provider to ensure the chosen adhesive will work effectively with your automated dispensing system.
Regulatory Compliance
Depending on your industry and application, it’s important to consider the regulatory compliance requirements when selecting a UV curing adhesive. These requirements ensure that the adhesive meets specific safety and performance standards for your application.
Biocompatibility for Medical Devices: For medical device applications, the adhesive must comply with biocompatibility standards to ensure the safety of the patients and users. Adhesives that meet ISO 10993 or USP Class VI standards are typically considered biocompatible and suitable for use in medical devices. Be sure to choose an adhesive that meets the necessary biocompatibility requirements for your specific application.
Flame-Retardant Properties for Aerospace Applications: In aerospace applications, flame-retardant properties are often required to ensure the safety and durability of the bonded assembly under extreme conditions. Select an adhesive that complies with flame-retardant standards, such as FAR 25.853 or UL 94, to meet the safety requirements of aerospace applications.
Other Industry-Specific Regulations: In addition to medical and aerospace applications, other industries may have specific regulations or certifications that need to be met. Examples include food and beverage, automotive, electronics, and more. It’s crucial to understand the regulatory requirements for your industry and select an adhesive that complies with these standards.
Finding the Right UV Light System for Curing Adhesives
Uvitron International is a leading manufacturer of high-quality UV light curing systems designed to provide efficient and reliable curing solutions for various applications. Our systems are compatible with a wide range of UV curing adhesives, ensuring that you achieve the best possible results for your bonding process. Our team of experts is committed to providing excellent customer support, guiding you through the selection process and ensuring that you choose the right system for your specific requirements. There are several reasons why customers should choose Uvitron International for their UV light curing needs:
Wide Range of Products: Uvitron International offers an extensive selection of UV light curing systems, including flood, spot, and conveyor systems. These are designed to cater to diverse applications and industries, ensuring that you can find the perfect system to match your specific requirements and budget.
High-Quality Systems: Proudly Made in the USA: Our UV light curing systems are designed using advanced technology and manufactured with high-quality components in the USA. This ensures reliable, efficient, and consistent curing results, while also providing a long-term solution for your UV curing needs.
Compatibility with Various UV Curing Adhesives: Uvitron International’s systems are compatible with a wide range of UV curing adhesives, making it easy for you to find the right adhesive for your application. This compatibility ensures that you can achieve the best possible bonding results with our systems.
Expertise in UV Light Curing Systems: With years of experience in the industry, our team of experts is well-equipped to guide you through the selection process and help you choose the right UV light curing system for your specific needs. This ensures that you can make an informed decision and find the most effective solution for your application.
Exceptional Customer Support: At Uvitron International, we pride ourselves on providing excellent customer support. Our team is always available to answer your questions, provide technical assistance, and ensure that you are satisfied with your purchase. We are committed to helping you get the most out of your UV light curing system.
Commitment to Innovation: We are constantly working to develop new and improved UV light curing systems, incorporating the latest advancements in technology to provide our customers with cutting-edge solutions. By choosing Uvitron International, you can stay ahead of the curve and ensure that you are using the most advanced and efficient UV curing systems available.
Page 6 of 11« First«...45678...»Last »